For more than 30 years, the process of creating synthetic insulation at PrimaLoft’s Vietnamese manufacturing facility was mostly unchanged. Webs of synthetic insulation would pass along giant conveyor belts, where they were teased by industrial-size hairbrushes and layered into sheets, before entering ovens the size of school cafeterias.
Intertwined in the tangle of polyester fibers was PrimaLoft’s secret ingredient: a proprietary synthetic fiber that has an extremely low melting temperature. When the insulation would reach its fiery fate, that binder fiber would begin to melt, locking everything together in a sheet. It’s the key differentiator of a puffy jacket or pair of mittens made with PrimaLoft: The insulation doesn’t need baffles (or stitched compartments).
A puffy jacket filled with natural down, on the other hand, needs baffling to keep loose feathers from shifting. The extra stitching of those baffles becomes a weak point in a garment: A seam can rip, a feather can slip through a stitch hole or the face fabric can tear where it’s been sewn through. But a puffy jacket made with PrimaLoft (and therefore no baffling) is inherently durable.
The Albany, New York-based brand has been making insulation in this same general way—with huge ovens churning through insulation sheets—since higher-ups from the United States Army approached it in the 1980s looking for a water-resistant alternative to down. Since then, PrimaLoft has gone on to produce synthetic insulation for a number of big-name outdoor brands like Patagonia, The North Face, Outdoor Research, Mountain Hardwear and more. But for years, designers at PrimaLoft have known the process holds a pretty major flaw: those ovens.
“Our technology creates a very effective material, but it doesn’t do it in an incredibly green way,” acknowledges PrimaLoft’s CEO Mike Joyce. The giant ovens in the brand’s Asian plants are powered by coal or natural gas, fuel sources that Joyce admits are among the largest carbon emitters in the textile industry at-large. And so five years ago, Patagonia approached PrimaLoft about finding a way to improve on the sustainability of the insulation maker’s manufacturing process.
“It was very clear from a study we did that those thermal-bonding ovens were the biggest culprits,” says Vanessa Mason, PrimaLoft’s senior vice president of engineering insulation and polymers. While brainstorming with Patagonia, PrimaLoft’s chief engineers began researching products used in the construction industry for rapid drying.
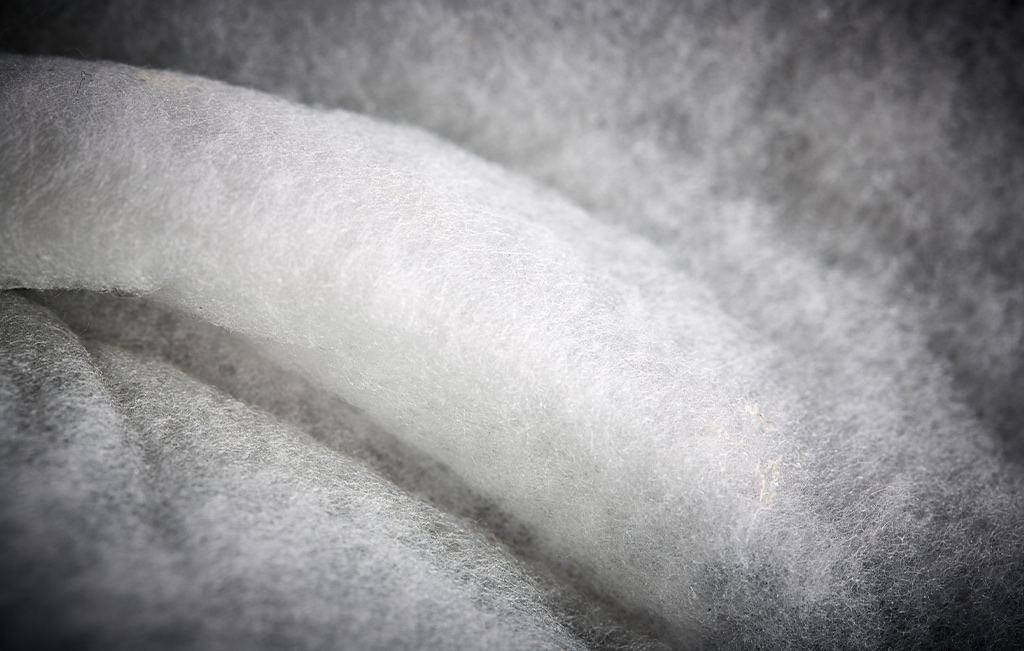
PrimaLoft P.U.R.E. insulation
After a year of research and development, the scientists figured out how to apply that tech to insulation. The new process, dubbed P.U.R.E. for “Produced Using Reduced Emissions,” ditches both the binder fiber and ovens altogether. Instead, PrimaLoft altered the composition of a resin spray, a common additive used alongside the binder fibers, to be reactive to oxygen. And so in lieu of ovens, the insulation can simply cure at room temp.
By shutting down those cookers, PrimaLoft cuts its carbon emissions from a single factory by 48 percent—a significant number given that the performance of the insulation isn’t affected at all, the brand says. The brand began transitioning all of its Vietnamese facilities to P.U.R.E. factories in 2018 and will follow suit with its others as soon as this year.
P.U.R.E. insulation is set to first hit shelves this fall in the venerable Patagonia Nano Puff. The Nano Puff (which has been around for a decade) is currently made with PrimaLoft Gold Eco, a synthetic insulation that includes 55 percent recycled content, but still requires the use of the ovens. With the move to P.U.R.E., each jacket will still be made with recycled materials while reducing emissions. “P.U.R.E. is now part of the impact reduction vocabulary,” says Matt Dwyer of Patagonia’s materials innovation team. “There is no magic bullet for apparel sustainability, but we’re excited to have another tool in our toolbox.” REI will carry the Nano Puff with P.U.R.E. in all stores and on REI.com beginning in September.
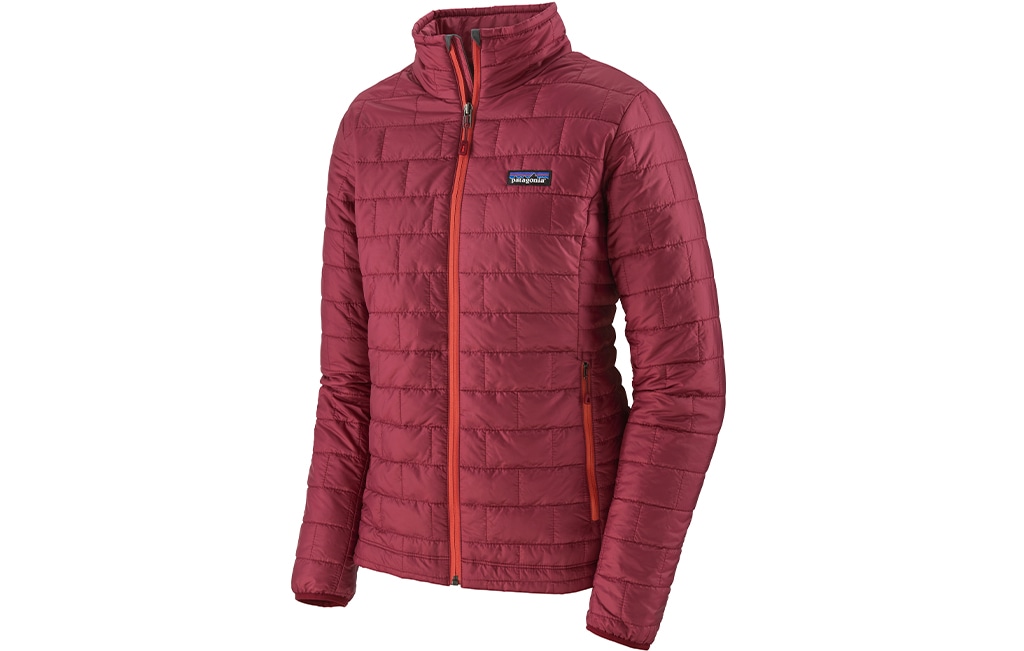
This September, find the new Patagonia Nano Puff with PrimaLoft P.U.R.E. at REI.
Eventually, Joyce expects to scale P.U.R.E. across PrimaLoft’s entire line, where it will proliferate across the industry for brands using synthetic-fill insulation. “We’re not just building our business,” adds Mason. “We want to support other brands as well, for the good of everyone.”
According to Mason, PrimaLoft will continue to monitor its carbon footprint and R&D ways to improve. “We don’t want to be a company that is dependent on fossil fuels,” she says. Taking its products to a point where they are fully recyclable is also on her radar; in 2018, PrimaLoft took the first step in that direction, introducing PrimaLoft Bio, the world’s first synthetic insulation made entirely from biodegradable fibers.
“We believe that you can have performance and sustainability without sacrificing either,” Joyce says. And with its track record of innovation and science, PrimaLoft may be in the best position to shake the industry.
For more stories of brands doing good work, visit our Good Gear landing page.